Cricket-mad Pakistan might not have much of a
football team -- 159th in FIFA's world rankings -- but Sialkot has a
long history of manufacturing top-class balls.
Forward Sports has been working with Adidas since 1995 and supplies
match balls to some of the world's top football competitions, including
the Champions League, the German Bundesliga -- and now the World Cup.
It is believed that a cobbler was once asked to repair a punctured ball
for colonial-era British soldiers, later studying how to make them.
|
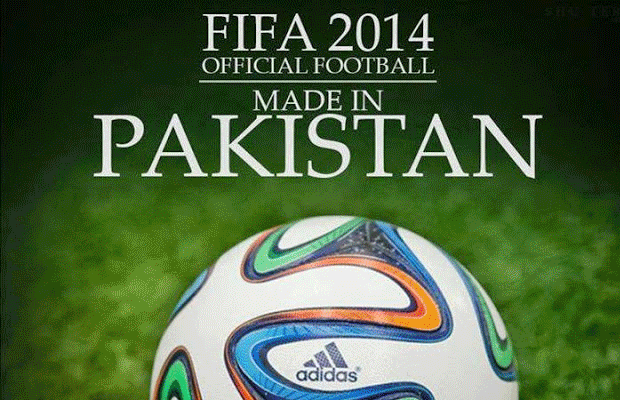 |
So began a successful business venture that spawned an industry, but
child labour scandals in the 1990s almost sank it.
Now international brands like Adidas work closely with factories and
NGOs to enforce stringent checks to prevent any return to the dark days
of children stitching balls in dingy backrooms.
At Forward Sports, workers must provide government ID to prove they are
over 18.
And while the basic 10,000-rupee ($100) monthly salary might put a $160
FIFA-approved "Brazuca" ball beyond the reach of the workers, several
spoken privately said the company looked after them well.
In any case, assembling modern match balls is not simply a matter of
sitting down with a needle and thread.
The Forward Sports plant stands barely a free kick's distance from the
dust and chaos of the Grand Trunk Road, the ancient highway that cuts
across the subcontinent all the way to Kolkata.
In contrast to the baking, deafening road outside where ancient goods
trucks, donkey carts and motorbikes overloaded with families and
livestock compete to avoid potholes, order and efficiency reign inside
the factory.
On the Brazuca production line, women in headscarves, some with their
faces veiled, work briskly.
|
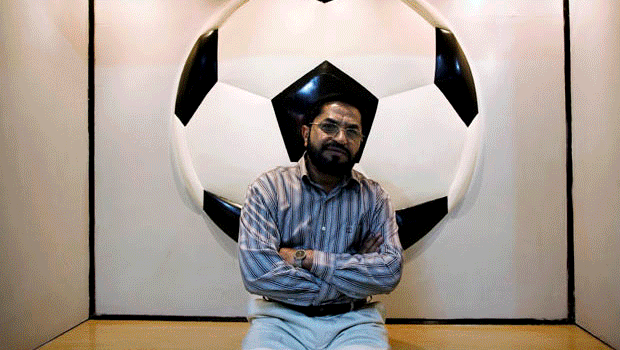
|
They start with flat white propeller-shaped pieces of polyurethane, add
the Brazuca's distinctive bright colours and glue the panels to the
ball's rubber bladder.
The seams are then treated with a special sealant and the ball is heated
and compressed in a spherical clamp to give it the correct shape. The
heat also activates the temperature-sensitive bonding compound that
holds the ball securely together.
The whole process from flat panels to finished item takes 40 minutes --
speed is crucial to prevent impurities getting into the ball -- and the
factory can produce up to 100 per hour.
It's a high-tech process for Pakistan, where much of the workforce is
unskilled and poorly educated -- only around half the population can
read and write.
|
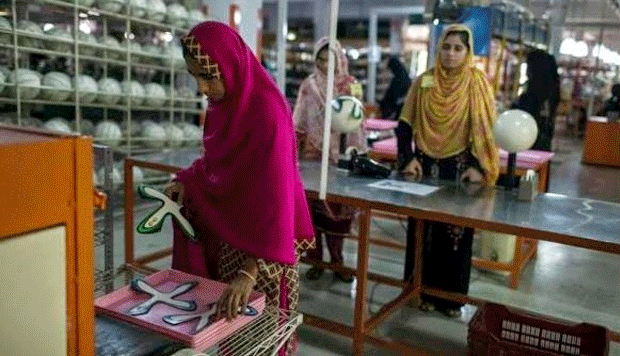
|
Ninety percent of those working on the Brazuca were women -- unusual in
Pakistan, where they are largely expected to stay at home with families,
but Akhtar said they were more diligent and meticulous than their male
colleagues.
Making the Brazuca was no simple matter for Forward, as Adidas gave the
order at short notice when they realised their main manufacturer in
China was unable to meet demand.
In just over a month, Forward managed to have the equipment it needed to
make the Brazuca from scratch.
Quality control is crucial, as the world's greatest football tournament
and greatest players demand the best equipment.
In the gleaming labs of Forward Sports, white-coated technicians put the
Brazuca, 437 grams in weight and 69 centimetres in circumference,
through a battery of tests on precision equipment brought from Germany.
|
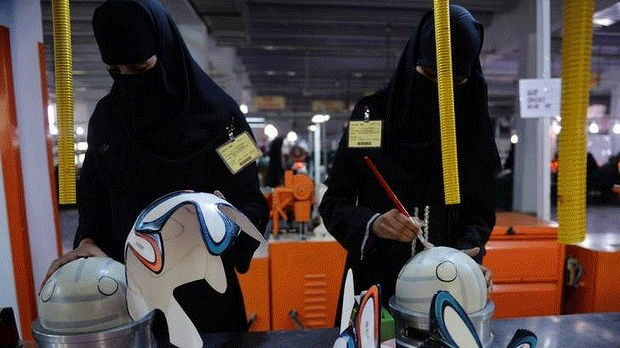 |
One machine rotates the ball while a curved arm tracks its surface,
measuring 4,500 points and plotting its shape in 3D on a computer to
ensure it is properly round.
Other devices measure bounce, resistance to water and mould, even the
glossiness of the ball's surface.
The ball's durability is also rigorously tested. A special machine fires
Brazucas at a flat metal plate -- they must survive 3,500 impacts at 50
kilometres (30 miles) an hour.
The Brazuca was designed after the controversy that dogged the Jabulani
ball at South Africa 2010 -- slammed for its erratic, unpredictable
flight. |